Table Of Content
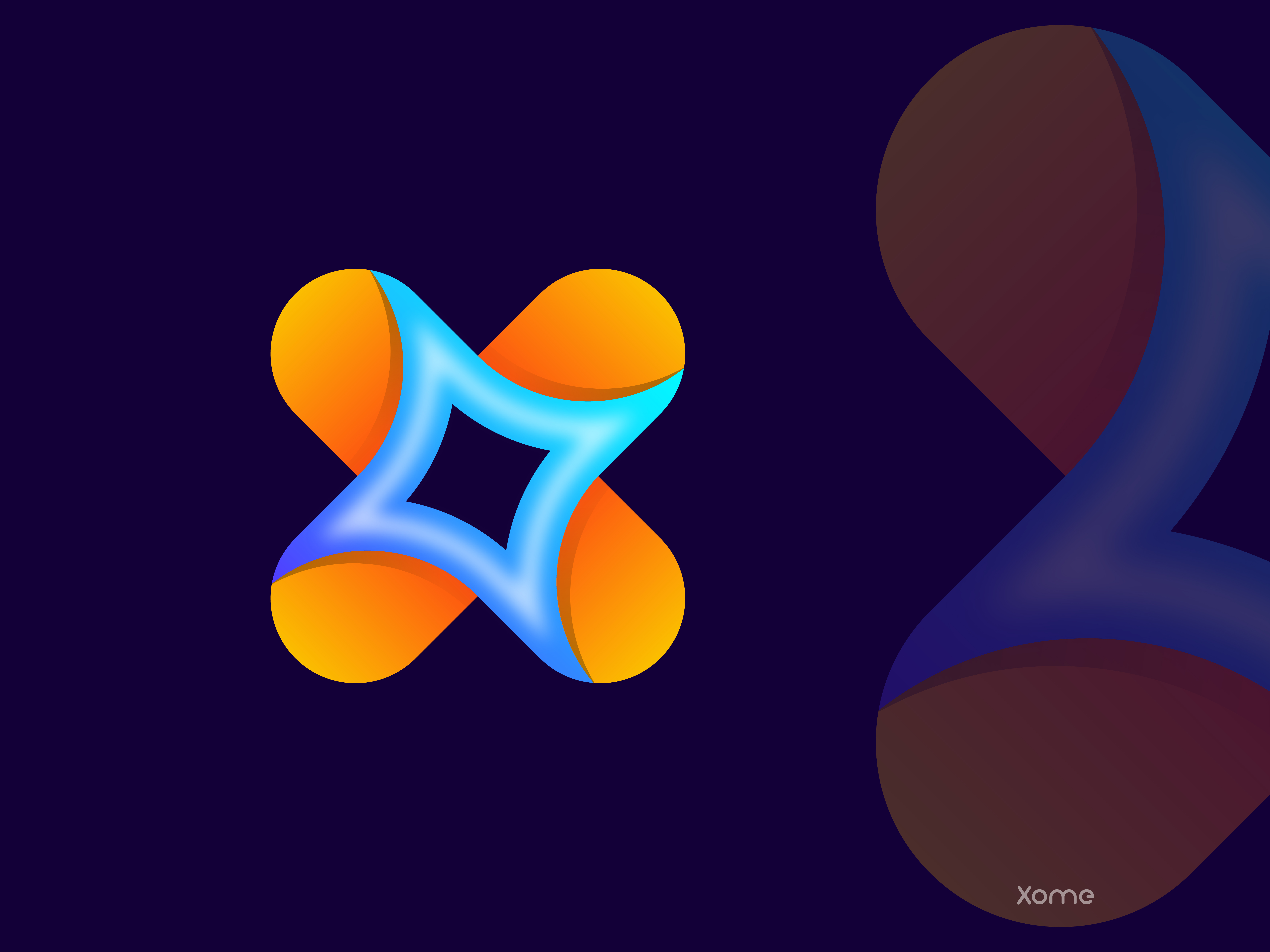
DFX approaches have considerable benefits for both companies and customers. By reducing waste and focusing on efficiency at every stage, companies can shorten the time to market and concentrate on fulfilling customer needs. This results in higher quality products that are available sooner, have less impact on the environment, are safer, more robust, and are tailored to deliver exactly what the customer expects of them. DFX techniques also ensure regulatory compliance which enhances quality, reduces warranty costs, and prevents product recalls. In project management, DfX principles help optimize product design by keeping key end goals in mind right from the start.
Products and services
Design of X-band SSPA based on GaN HEMT for telemetry subsystem of near-earth space missions - ScienceDirect.com
Design of X-band SSPA based on GaN HEMT for telemetry subsystem of near-earth space missions.
Posted: Fri, 30 Apr 2021 07:02:42 GMT [source]
The Potter Daniels Manor, the English Tudor Revival–style residence that hosted the 1975 and 1996 showcase houses, has been reimagined with 30 new interior and exterior spaces for the 2024 edition, which is now open until May 19. Our professional in-house designers review and repair every order we receive to ensure each one is printed to perfection. Get inspired by some of our happy customers and their t-shirt designs.
Design for Testing (DfT)
A way to do this is by building in systems that show the real-time condition of a product. The sight glass allows for an engineer to check the oil level regularly and prevent any major breakdown. DFX reduces the number of tools needed for design by limiting it to a standard set for increased efficiency. This is one of the areas DFM (design for manufacturing) touches upon. Designers Frank Slesinski and Serena Brosio collaborated on the charming living room in the Gatehouse. “One of the main things we did was add a window seat, which looks like it should always have been here,” Slesinski says.
Apple Watch
The software effectively takes the boundary conditions and optimization target and designs the part from scratch (or from a very rough base representation of the part). It’s basically taking the inputs, running mechanical simulations, adjusting the design based on the output, and iterating on that process until an optimal result is achieved. Design for ergonomics – make the product very appropriate to the user’s body in order to be eminently usable. The product has to perform as expected by the user throughout its expected lifespan, and that may require some periodic and planned downtime (e.g. oil check on a car). A large printing machine shows its real-time status as well as a diagnostic, and that’s very useful to users. Ordering and installing replacement parts easily and quickly is a major benefit to users.
Conventional Product Development Process
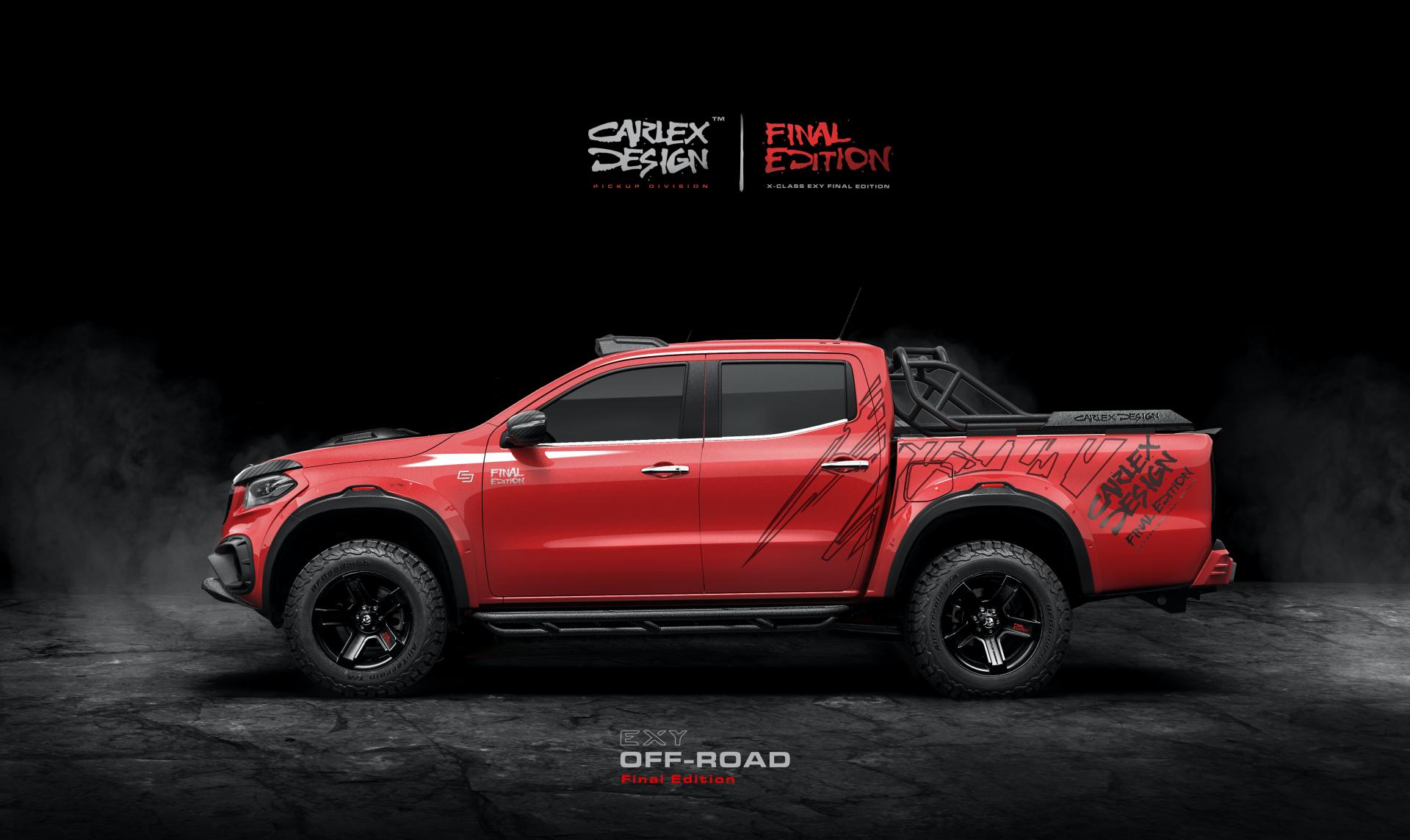
Another important feature that improves maintainability is developing a modular product. The ability to order and replace just the failed parts is an attractive feature for any product. There are many other tools also available at a reliability engineer’s disposal.
A Snow Storm for X-mas - Article onThursd - Thursd
A Snow Storm for X-mas - Article onThursd.
Posted: Sat, 25 Dec 2021 10:47:32 GMT [source]
The different types of DFX methodologies
Today’s supply chain rumor comes from Digitimes and says that a next-generation Apple Watch will use a new resin coated copper (RCC) motherboard design. Samatha Williams’s Tearoom in the Gatehouse is brimming with vintage charm and elegant accents. Working with Jacqueline Black and Michelle Porreca, Williams brought in a Chinoiserie wall covering to give the space a garden-like atmosphere. They also installed a grass cloth ceiling treatment and sisal rug to add texture. Maria Videla-Juniel, who designed the primary bathroom of the main house, also devised a welcoming entry to the Gate House.
Design for Product Life Cycle
It is not necessary to use all the tools for every part but only ones that apply for a certain use case. DFM focuses on the fabrication of a product/component, whereas DFA focuses on the product architecture.
Third, you will probably commit to delivering products similar to your first look-good prototype, and it means you should confirm all the materials, processes, etc. by that point. Asking all of these questions in the initial product design, and then at every important milestone, is a way of detecting issues while they can still be addressed without excessive cost and delays. By considering the overall cost of the product and engineering lower costs into the product from the initial stages of design, unnecessary costs can be prevented.
DFX with an impact all the way through the product lifecycle
Despite serving as one of the largest sports markets in the United States, Chicago has never hosted an NFL title game, a goal NFL commissioner Roger Goodell indicated in February would require the construction of a domed stadium. The proposed project will cost $4.6 billion, with half the total funded by taxpayers, according to a Wednesday report by the Chicago Tribune. Apple is reportedly working on an Apple Watch overhaul that could be dubbed the “Apple Watch X.” Apple announced the Apple Watch in September 2014, so we are approaching its 10-year anniversary.

Designer Ashleigh Miranda focused on juxtaposing technology and earthy elements in her moody media room. Bursts of hot pink and apple green energize Steven Cordrey’s design for the home’s veranda. Hand-beaded light fixtures illuminate the seating areas, which feature tables and chairs from Janus et Cie’s Amalfi Coast outdoor collection. The t-shirts got here a week before our event, so we weren’t scrambling or worried and they ended up just like the mockup on the website.
The product supply chain should be considered during the product design stage. This clarifies inventory requirements, reducing supply chain costs, lead times, and wastage. Errors are detected and corrected after the design phase in the traditional engineering design process. For a long time, the supply chain for a product was always an afterthought.
This leads to better employee engagement across all levels, encourages supplier collaboration, and enhances product usability, product safety, and, ultimately, customer satisfaction. Creating a quality product that is efficient, reliable, and durable requires a deliberate and methodical approach to the design phase. Design for Excellence, or DFX, is a methodology that was developed to specifically address the issues of waste involved in traditional engineering processes. DFX aims to provide a method where you can optimize your products during the initial stages of their development. Using the DFX methodology means that you can avoid having to make expensive and time-consuming changes during pre-production or even at the post-production stage. Implementing a DFX system requires a significant change of mindset within a company.
No comments:
Post a Comment